2016年11月11日
インダストリー4.0最新動向、日本・ドイツ・アメリカが目指す未来とは
デンソーが考える、工場から広がるIoTの世界 「ダントツ工場」の主役は「人」だ!
価値を生み出す取り組みをサプライチェーンに広げていくのが狙い
──2020年までに、生産性を2015年比で30%高める目標ですが、現段階ではどのあたりに取り組んでいるのでしょうか。
加藤氏:
現段階では工場同士をフィジカルにつなげることに注力しています。生産性向上は3段階のフェーズで進めていくことを考えています。
第1段階では、IoTによる見える化で、ボトルネックを可視化します。第2段階では、可視化したデータを多角的に再分析、ビッグデータ解析等も用い、ボトルネックを解消。止まらない、不良を作らないラインを目指していきます。ここまではロスミニマムを達成する段階です。
生産性を30%高めるにはもう一段階必要です。自社の力、自社工場の力を超えたところで稼働率を高めるということです。自社の知見や過去のやり方だけにこだわらず、事象によっては他社のベストプラクティスを参照、活用することによって、これまでと異なる質の改善、改良をなし得ていくことです。
──データの分析を含めて他社との協業はどのように進めていきますか。
加藤氏:
デンソーはモノづくりの会社ですから、フィジカルなモノづくりの知見は多々ありますが、サイバーの世界に関する知見はそれほど持ち合わせていません。
自分たちに必要なシステムは自分たちが一番わかっていますし、要件定義のところまではできるのですが、グローバル標準で最適なシステムを作り込んでいく部分は経験薄ですし、十分な技術を保有していません。そこはノウハウをお持ちの他社との協業で補っていくことを考えています。
IoTの世界は、自分たちがわからないところはオープンにして、「力を貸してください」といったほうが、より多くの知見やノウハウを得ることができます。またその数が多ければ多いほど有益な情報を入手する可能性が高くなります。それによってスピードも出るし、より価値も高まっていくはずです。
──今後の価値創造の中で、IoT革新室が果たすべき役割とは何でしょうか。
加藤氏:
IoT革新室は情報を活用しモノづくりの力を向上させることがミッションです。その際の重要な考えは、新しい設備などだけが情報活用できる姿にするのではなく、今までの有形資産もさらに有効活用できるようにしていくということです。
新しい工場、ラインをスクラッチで設置する際に最初からIoT技術を使う前提で設計し、導入していくことは一つの方法です。しかし、我々が目指す130工場をつなぐというのは、今の資産をもっとスマートにし、活躍させるという話でもあるのです。
例えば、中小企業の皆さまは、これまで何十年と使っている設備をしっかりメンテナンスして大事に使っています。それがIoT化するから新規設備に入れ替えるということにはなりません。大企業だけ、限られた企業だけがIoTでスマート化するという世界は、デンソーは望んでいません。
日本のモノづくりの底上げにIoTを活用する、デンソーはそこに貢献したいと考えています。弊社のラインも、古い設備は、通信プロトコルもバラバラで、フィジカルにつないでもデータが連携できません。
そこで、バラバラのプロトコルを一つの共通プロトコルに変換するミドルウェア「ORiN2」を開発しています。それを介せば、どんなに古い設備、機器でも通信できるようになります。
共通プロトコルでつながったデータを使い、分析・処理すれば、IoT化でき、有益であることを、まず自社の中で実証していきたいと考えています。その事例、ユースケースをどんどん試行し、中小企業の皆さまにも早くご提供できるよう努力していきたいと思っています。
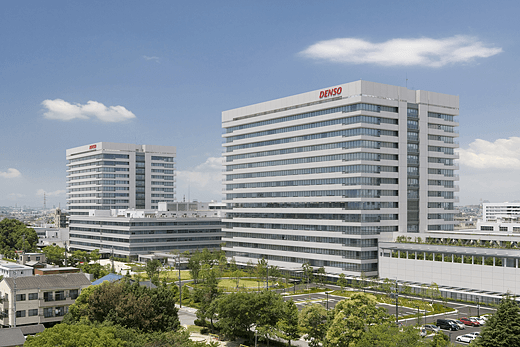
「モノ」の捉え方によってIoTの意義は変わってくる
──欧米の動きをどうご覧になっていますか。
加藤氏:
IoTの着地点は、結局のところ、「モノ」を消耗品と考えるかどうかで変わってくると思います。例えば、工場のロボットの中にはギア、モーターといった消耗品が組み込まれ、複合的に稼働しています。これらの消耗品を予兆管理で適切に交換すれば、抗耐久品として扱うことができます。
この稼働に伴うメンテナンスで対価を得て、消耗品を抗耐久品化させるというビジネスモデルの変革がIoTで起きようとしています。ボッシュは抗耐久品のモノづくりのビジネスを売却していますし、シーメンスもGEも「消耗品」の入れ替えによって「抗耐久品」に変えるビジネスにシフトしています。
一方で、最初から精緻なモノづくりをして、15年間メンテフリーで壊れない製品を作るというビジネスも依然として存在し続けるでしょう。簡単に交換できないモノというのはありますし、例えば車は、途中で止まってはいけないので抗耐久品でなければなりません。
我々は車の部品、抗耐久品を作るビジネスですから、一気に「消耗品から抗耐久品へのビジネスモデルのシフト」を進めることは考えていません。
一方で、Uber社が進めているようなシェアリング化は注視する必要があります。ビジネスモデルの変化により、車の稼働率が上がるといわれていますが、そうなると従来のような「15万キロ保証」ということではなく、車がどんどん消耗品化し、交換しながら使っていくという流れになるからです。
──海外での「ダントツ工場」構築については、日本の品質に対する要求をどこまで求めていくお考えでしょうか。
加藤氏:
我々の会社の理念には「人を大切にする」「地域で共生する」というビジョンがあり、それをベースに考えたいと思います。ベースとなる標準的なIoTの枠組みは必要ですが、その先には、地域なりの最適なやり方を尊重したいのです。
つまり、拠点の成熟度、地域の成熟度にあわせてグローバル化とローカル化のバランスをとっていくということです。一律的に、こうあるべきだという解はありません。地域、事業の特色、拠点の成熟度によって、バランスの置き方は変わってきます。今や海外生産比率は50%を超えており、今後、需要として増えていく傾向にあるのは間違いありません。
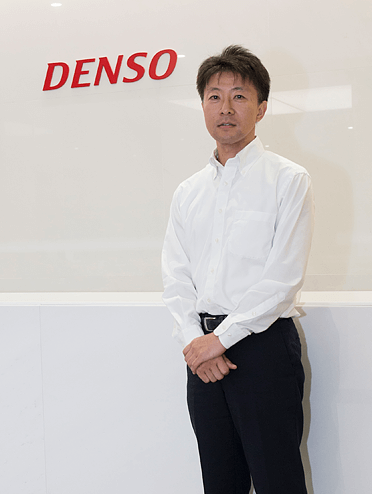
──最後に、デンソーのIoTへの取り組みについて、改めて今後のロードマップをお聞かせください。
加藤氏:
短期的視点となりますが、データ分析の力を向上させることは重要だと思っています。大量のデータを処理できるビッグデータの活用については、企業競争力に直結するため力を入れています。国内だけでなく海外の大学とも連携して取り組んでいます。また、デンソーには国内に18の製造部門がありますが、そこでボトルネックになっている工程を、データドリブンで最適化するプロジェクトにも取り組んでいます。
海外のいくつかの工場でも、トライアルを開始し、早い段階でグローバル規模にまで拡張していきたいと考えています。
一方、130工場をIoTで連携させる取り組みについては、今年は複数の工場、来年は二桁の工場をつなぐ目標で取り組んでいきます。2020年までに130工場ですから、ステップを刻んで確実に取り組んでいかなければなりません。
製造現場は生き物なので、見れば見るほど、リアルタイムでデータを取っていかないといけない場面が多々あります。
当然、投資と多くの工数を伴いますから、IoTで実益を出すための工夫は試行錯誤の連続です。しかし、機械で行うべき「定常」領域と、人が介入すべき「非定常」領域の見極めができれば、絶対にIoTは有益なツールになると信じています。
試行錯誤のスピードをもっと高め、人と設備が共創するダントツ工場を、同じ夢を共有するグローバル拠点の仲間たちと一緒に作り込んでいきます。
──本日は、貴重なお話をありがとうございました。
(インタビュー=フロンティアワン 代表取締役 鍋野 敬一郎、ビジネス+IT 編集部 松尾慎司)