2017年02月24日
工場の「無線IoT化」が日本の製造業を飛躍させる
──製造現場における無線実証実験プロジェクト
現場の要望を踏まえて進められる実験
このプロジェクトがユニークなのは、実験のほとんどが研究室ではなく、三菱重工工作機械、トヨタ自動車などの稼働中の工場で、現場の要望を踏まえながら進められていることだ。
「それぞれの工場には、IoTによって実現したいニーズがあります。そのニーズに合わせて実験系を組んで検証する。それがこのプロジェクトの方針です。」
例えば、生産ラインの中のAという機器とBという機器をつなげたい、あるいは有線でつながっていた両機器の接続を無線化したいという工場側の要望がある。その場合には、実際にAとBの間での無線通信を行い、データを集め、検証する。板谷氏らプロジェクトメンバーは、一つの工場に何日間も張り付くことが必要な、そんな地道な実験にこの1年の間取り組んできた。
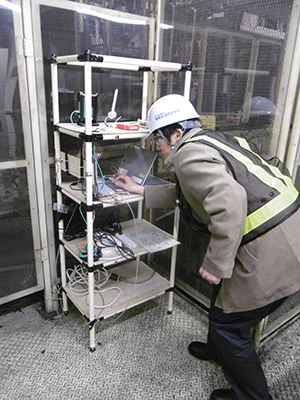
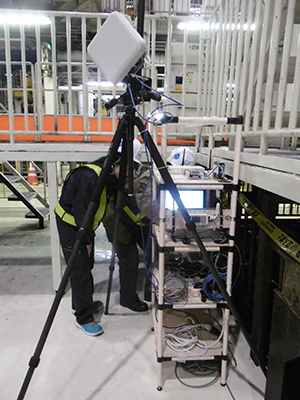
様々な工場で無線環境の実証実験を実施
実証実験の最大のメリットは、生産現場の現実に即したデータを取得することができるということ、そして、そこから実用にダイレクトに結びつくソリューションを生み出すことができるということだ。「このような方法で数多くの工場で実験を行い、データを収集している取り組みは、世界的に見ても非常に珍しいと思います。」と板谷氏は胸を張る。
現場での実験は、想像もしなかったことを明らかにすることがある。例えば、数多くの機器が稼働し、物や人が絶えず動いている工場では、無線環境がダイナミックに変化していることが実験で分かったという。
「建物の中に無線のつながりやすいエリアとつながりにくいエリアがあるばかりでなく、そのエリアは刻々と変化していることが明らかになりました。また、その工場の規模や設備内のレイアウト、近隣に住宅があるかないかといった条件でも無線のつながり方は変わります。無線環境の変化がここまで激しいとは、正直思ってもみませんでした。」
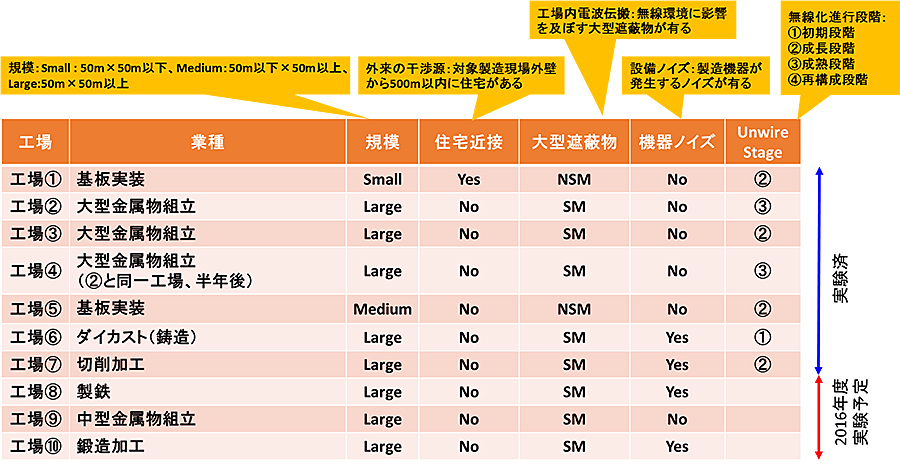
工場の規模、住宅地が隣接する立地か否か、工場内の大型遮蔽物の有無、設置ノイズの有無、無線化発展段階(Unwire Stage)の属性によって分類したもの
画像を拡大する
混線を防ぎ、データを選別する
現場での実証実験は2017年3月でいったん終了し、4月以降は、これまで集めてきたデータをもとに無線システムのプロトタイプをつくり、それを工場でシミュレーションしていくフェーズに入っていく。システムの鍵となるのが、工場内に飛び交う数多くの無線が混線したり干渉し合ったりしないような仕組みづくりだ。そこにプロジェクトに参加している企業の技術力やノウハウが生かされることになる。
さらに、IoTによるデータ収集の方法にも、独自の工夫が施されることになるという。
「IoTを導入すると、“とりあえず、すべてのデータを取っておけ”という方針になりがちです。しかし、生産現場で発生する大量のデータをすべて無線で収集しようとしたら、周波数の帯域があっという間に埋ってしまいます。その結果、無線がつながらなくなる機器が発生し、生産ラインがストップしてしまうこともありえます。」
そのようなリスクを防ぐのが、ゲートウェイを設置し、そこでデータを選別していく仕組みだ。
「どのデータが重要で、どのデータがそうでないかは、生産現場によって異なります。それを判断して、必要なデータだけをクラウドに送るインテリジェンスを構築する必要があります。分析の観点からも、そのようなデータ選別の仕組みは必須と言えます。」
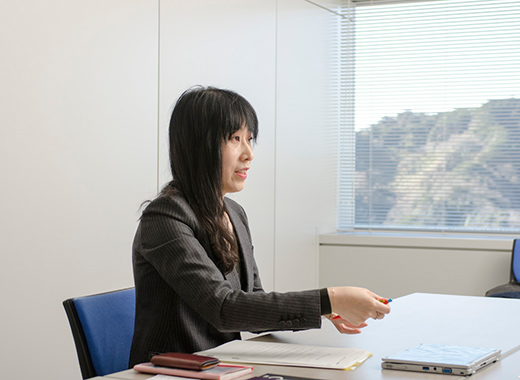
さまざまな国で活用できる仕組みを
このプロジェクトが将来的に目指しているのは、どのような規模の、どのような業種の工場でも汎用的に利用できる無線システムを開発することだ。その基幹技術を参加企業が力を合わせて固めていく作業がこれから進んでいく。しかし、それを「日本発の技術」、あるいは「日本発の無線規格」とアピールしていく気はないと板谷氏は言う。
「日本がリーダーシップを取りながらも、世界各国の標準化グループや企業などと柔軟に協力し合って、さまざまな国で活用できる仕組みをつくることを目指しています」
ここでも「柔軟性」が重要なキーワードとなっているわけだ。当面構想されているのは製造現場に特化した仕組みだが、システムが完成すれば、工場以外で利用できる可能性もある。例えば、空港施設、船舶内、病院など、一つの空間の中にさまざまな機器がひしめき合う場所での利用が想定されるという。
「今後、工場での検証を重ねながら、2020年をめどに実用化に漕ぎつけたいと考えています。」
戦後の日本の経済成長を牽引したのは製造業だった。だが1980年代以降、日本の多くのメーカーが人件費の安い海外に製造拠点を移し、国内の製造業の空洞化が進んだ。日本の「お家芸」であるものづくりを守ろうという機運が再び高まってきたのはここ数年のことである。工場の「無線IoT化」は、その動きに拍車をかけることになるだろう。プロジェクトの先行きに大いに注目したい。