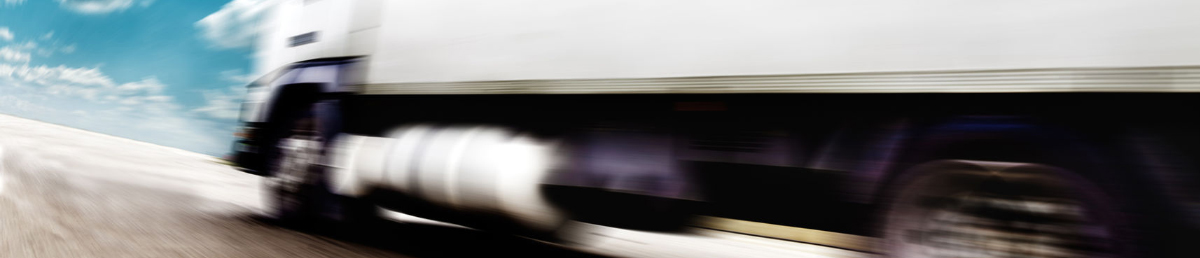
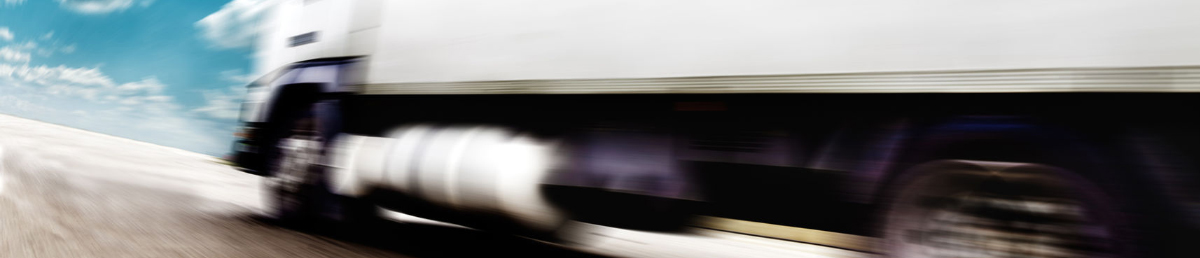
製造業のサプライチェーンマネジメントには
なぜ「物流改革」が欠かせないのか?
ものをつくって売る──。製造業のビジネスは端的にそのひと言に集約されるが、「物流」という機能がなければそのビジネスは成立しないということがしばしば見過ごされている。ものをつくるためには部品の物流が必要であり、ものを売るためには製品の物流が必要である。しかし多くの場合、生産と物流はまったく別々のプロセスと考えられている。ものづくりと物流を一体のサプライチェーンとしてとらえ、その全体をいかに最適化していくか。そのような課題にNECが直面したのは90年代だった。NECが取り組んだサプライチェーンマネジメントとその成果について、日通NECロジスティクス社長付主幹の鳥井 恭 氏が語った。
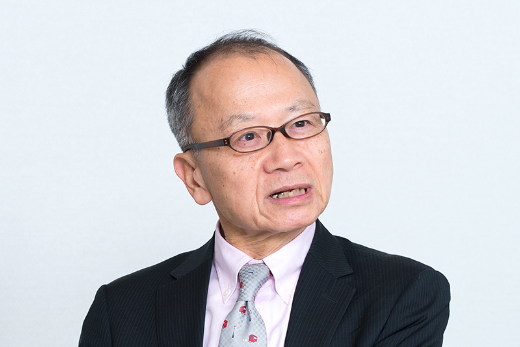
NECものづくり革新ユニット 生産技術開発部長、
日通NECロジスティクス 取締役執行役員常務を経て、
現在、日通NECロジスティクス 社長付 主幹
生産革新からサプライチェーン革新へ
日本の製造業が生産拠点を海外に移す動きが加速したのは、大幅な円高が進んだ1990年代のことだった。数多くのメーカーが生産コストの安いアジア地域に次々に工場を設立し、日本のものづくりの空洞化が叫ばれ始めた。
同時に製造業の事業環境も大きく変化していた。製品をつくれば売れる幸福な時代が終わりを告げ、つくる側から買う側に市場の主役の座が移ろうとしていた。多様化するユーザーのニーズに応じた製品を迅速に生産し、迅速に届けること。それがメーカーの課題となった。いわゆる「多品種少量生産」と「短納期」の始まりである。個別受注生産(BTO:Build to order)の仕組みを本格的に導入するメーカーが現れたのもこの頃からだった。
海外工場とのコスト競争と、多品種少量生産・短納期化への対応──。その課題に立ち向かうために、80年代の自動化FA化を経て、NECも国内工場の生産革新に着手した。トヨタ生産方式(TPS)を最初に導入したのは93年頃のことである。当時、NECの生産システム研究開発部門で、NECの工場の生産革新に携わった鳥井恭氏は振り返る。
「当初、私たちは工場内の生産ラインの生産革新に取り組み大きな成果もありました。しかし、何かが足りませんでした。それがサプライチェーン、特に物流改革だったのです。TPSの本質は、物流再構築を含むサプライチェーン全体の最適化にあります。そして2000年、外部コンサルタントを招聘し、物流改革からトータルなサプライチェーンマネジメントに取り取り組み始めたのです。「当時、電子機器や精密機械のメーカーで、物流に着目してSCMに本格的に取り組んでいる企業は殆どありませんでした」
「タクシー型物流」を「路線バス型物流」に転換する
それまでは切り離して考えられていた「ものづくり」と「物流」を結びつけ、その流れを最適化すること。それがNECのSCMのビジョンとなった。しかし、なぜ物流が重要だったのか。
「以前の部品調達は、所要予測に基づいた計画に基づいてサプライヤーに発注し、自社の工場で部品在庫を抱えるという方法を採っていました。一方、製品も、実需ではなく月単位の生産計画に基づいて製造し、完成品をひと月から、ふた月の間倉庫にストックしておくことも珍しくありませんでした。しかも、部品や製品に欠品が起きる可能性があるのでさらに多く買い込み、仕込む。そんな悪循環が繰り返されていたのです。部品、製品の在庫が増えれば、キャッシュフローが悪化し、倉庫代など物流費もかさみます。結果、有利子負債も増大していました」
TPSでは、「短く単純な流れを作る」ことを徹底的に追求する。サプライヤーからの「調達物流」、工場での「生産」、お客さまにお届けするまでの「販売物流」といったサプライチェーン全体をとらえ、これが粛々と自律的、規則的に流れるような仕組みをつくること。さらに、この流れを工場の「生産計画」を中心としたプッシュ型から、川下に当たるユーザーの「注文」起点とするプル型に変えること。その2点がこの仕組みの大きなポイントである。
「まず、お客さまに納期に合わせて、お届けする物流便を決め、それに合わせて製品出荷のタイミングを決める。さらにそれにジャストインに合う生産をし、予定の物流便に乗せる。これが、いわば物流がタクトを振るプル型のサプライチェーンの考え方です」
この流れを淀みなく実現するために必要なのが、「定時・定ルート」の物流ネットワークである。NECのサプライチェーン改革は、工場の変革と足並みを揃えて、早い段階から「全国の輸配送物流ネットワーク作り」に着手した点が特徴的だ。
「それまでの物流は、必要な時にそのつど手配し直送する“タクシー型”でした。これを決まった時間に決まったルートを回り、多様な荷主の部品も製品も混載する“乗り合い路線バス型”にすることによって、何日の何時の便に荷物を載せれば、お客さまや工場に製品や部品がジャストインタイムで届くことがわかるようになります。安全をみて早めに作ったり早めに乗せたりする必要もなくなりました」
この物流ネットワークを整備すれば、例えば、別々の工場でつくっているPCとサーバーとルーターとプリンターを同じ便で顧客のもとにまとめて届けるといったことも可能になる。いわゆる「クロスドック」を活用した「品揃えの同期」を図る仕組みである。さらに、部品を工場に運んだトラックに製品を乗せて運ぶ「高積載の往復便」も容易に実現することになる。これによって、「トラックが空気を運ぶ」という非効率極まりない事態が改善し、結果、物流費の改善にも繋がるのである。
定時・定ルート網は、いわば血液がスムーズに循環する仕組みである。これによって血流の滞り、すなわち在庫が極小化される。注文に合わせて必要な数だけ製品をつくり、生産に合わせて必要なだけ部品を購入、もしくは使っただけ小刻みに補充することが可能になった。
注文から納品までのリードタイムが大幅に短縮
この仕組みの導入は大きな成果をもたらした。まず想定通り、部品と製品の在庫が減ることで、キャッシュフローが好転した。倉庫も大幅に削減された。削減率は倉庫面積にして6割に上った。また、物流効率が上がることで、一時は最大日当たり1200台だった運行トラック台数も4割削減された。
そればかりではない。上記を前提とした新しいITシステムの導入で営業部門が生産部門と共通のSCMの仕組みのもとで一体になって動くことが可能になり、ワークスタイルが目覚ましく変わった。
「以前、営業担当は、お客さまからのオーダーを元にいろいろな指示や確認を工場や物流部門にばらばらに伝えなければならず、進捗確認や社内調整にたいへんな労力を費やしていました。新しい仕組みでは、オーダー情報がサプライチェーン内でただちに共有されるので、そういった仕事がほとんど必要なくなったのです。営業担当の納期調整などの事務作業工数は、実に30分の1にまで減りました」
では、この新しい仕組みによる顧客側のメリットはどのようなものだったのだろうか。鳥井氏がとりわけ強調するのは、その成果である。
「注文から納期までのリードタイムが保証できるようになり、納期遵守率が100%になり管理不要になりました。さらに、リードタイム自体も大幅に短くすることができました。例えばPCの納品のリードタイムは、それまでの3週間から最短2日に短縮されています。これは当時、業界最短の納期でした」
このSCM改革は、さらに海外にも広がっていった。北米のNECの販売会社から需要の見込み情報、実売・在庫情報をタイの工場に伝え、売れたぶんを補充していくことによって在庫を削減する「グリーンベルト方式」と呼ばれる方法が確立した。
SCM改革にも物流改革にも完成形はない
NECのSCM改革は、キャッシュフロー改善や有利子負債削減を目標とした経営改革となった。まさに営業、開発、調達、生産、物流、スタッフといった全社を巻き込む経営改革であり、その中にあって意外なことに物流改革が最初に着手すべき最重要な施策になったのだ。ここで強調したいのは、物流改革とは単なる物流費削減ではなく、戦略的物流(ロジスティクス)機能の強化だったということ。ここを勘違いしている企業は未だに多くある──。10年前にNECを離れ、現在は日通NECロジスティクスの社長付主幹を務める鳥井氏はそう話す。
「物流を含むサプライチェーン全体を最適化することによって、工場のみならず全社員の生産性を上げ、ワークスタイルを改善し、お客さま満足度を向上させること。それがSCM改革の本来の目的であると考えています。つまり、SCM改革とは、製造業がこれからも力強く活動を続けていくための経営戦略なのです。そして物流(ロジスティクス)は付加価値を生む競争力の源泉として再認識されねばならない、と」
90年代半ばにNECが直面した課題は、決して「過去の課題」ではない。それから20数年の間に、その課題があらゆる製造業に広がっていったのだと鳥井氏は言う。
「現在は、一品一品異なるものを、以前のマスプロダクションのように最高効率、最高品質、最短納期でつくっていく高度なマスカスタマイゼーションの時代です。この時代には、まさしくサプライチェーン全体を最適化するマネジメントが広範な製造業に求められるのではないでしょうか」
物流業界に目を転じてみれば、EC市場の拡大などによって出荷量が増加する一方で、ドライバー不足が深刻な課題となり、いっそうの効率化が求められるようになっている。その解決策として広まりつつあるのが、異なる企業同士で物流を共有する「共同物流」の仕組みだ。
「輸配送を効率化するためには、運搬車両の積載率を上げる必要があります。その点で、共同物流は有力な解決策となるでしょう。最近では、競合企業同士の共同物流も実現するようになっています。物流は戦う場ではなく、共創する場。そう考えるべきだと思います」
「ものをつくって売る」という営みにはSCMが必須であり、そこに「形あるものが移動する」というプロセスがある限り、物流を抜きにしたSCMはあり得ない。NECは、「次世代ものづくり」を目指して日本の製造業が強くなるためのコラボレーション基盤として「NECものづくり共創プログラム」を運営しており、上述した「共同輸配送物流ネットワーク」など、これらの改革の実践に裏打ちされたノウハウやメソッドをアセットとして提供、共有している。
「製造業を取り巻く環境も、製造業というビジネスモデルもこれからも変わり続けるでしょう。したがって、SCM改革にも物流改革にも完成形はない。これからは、企業や業界の枠を越えて共創していく時代である。そう私は考えています」
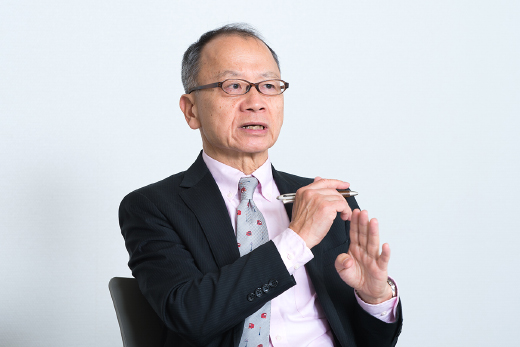