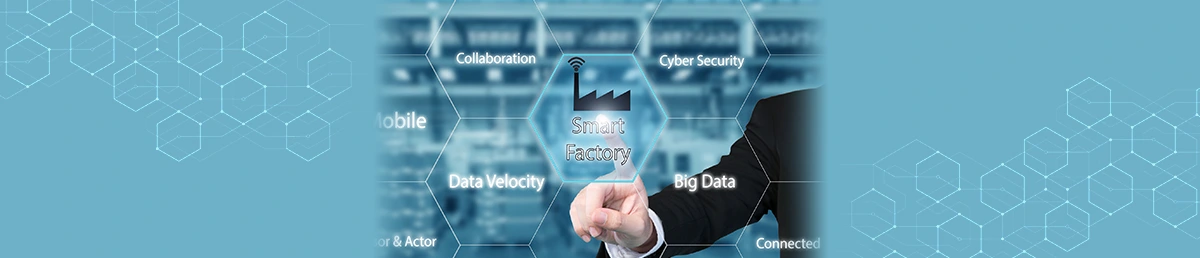
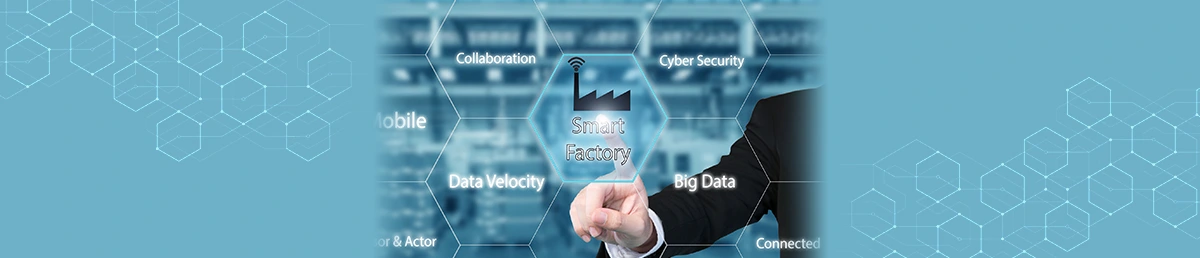
New Normal時代、住友ベークライトが目指すものづくりの未来
劇的な環境変化に直面する日本の製造業では、イノベーティブな業務変革を進めていくことが喫緊の課題となっている。こうした課題を解消するため、住友ベークライトはデジタルトランスフォーメーション(DX)を決断。NECとの共創により、国内主力4工場の生産設備の稼働情報をIoTで可視化するとともに、AIを活用した生産ラインの異常予兆検知と自律制御を実現した。これにより「人手に頼らないものづくり」の実践が可能となり、グローバルな競争力強化につなげる取り組みを加速させている。
劇的な環境変化を受け、ものづくりもデジタルシフトが不可欠に
製造業でのスマートファクトリーへの取り組みが加速している。その背景には、日本のものづくりを取り巻く劇的な環境変化がある。少子高齢化に伴う人手不足に加え、多品種少量生産や製品ライフサイクルの短縮化、季節や特定のイベントによる生産量の急激な変動などはその代表例だ。
こうした中で製造業も変わっていくべきだという考え方は、既に誰もが認識していたが、DXへの対応を始めていた日本企業は、それほど多くなかった。しかし、そこに予測もしなかった事態が起こった。新型コロナウイルスが襲来し、人の距離感や働き方、国同士の行き来や関係性など、社会の在り方が大きく変わったのだ。
製造業も例外ではなく、海外サプライヤーからの部品供給が途絶えたり、作業者を確保できなかったりと、かつてない状況に見舞われている。この猛威が収まっても社会は元通りに戻るわけではない。ものづくりの現場にもデジタルシフトが求められ、New Normal時代を生き抜くために、企業変革の必要性と重要性が今、改めて高まっているといえるだろう。
こうした劇的な環境変化にどのように対応するか――その有効なアプローチの1つが、IoTやAIを活用して生産ラインの効率化を実現する「スマートファクトリー」である。実際に、そうしたDXへ挑戦する企業も出てきている。住友ベークライトはその1社だ。
同社は、日本で初めてプラスチックを製造したパイオニア企業をルーツとしている。社名でもある「ベークライト」とは、数あるプラスチックの中で最も歴史の古いフェノール樹脂の商品名である。現在は、自動車や航空機の部品・成形品などに使われる「高機能プラスチック」、スマホやスマート家電に使われる「半導体関連材料」、医薬品や食品の包装材、医療機器を中心とした「クオリティ・オブ・ライフ」の3セグメントでグローバルに事業を展開しており、アジア・北米・欧州など海外向けの売り上げが全体の6割を占めている。
住友ベークライトが抱えていた大きな課題とは
ほかの製造業と同様に、住友ベークライトも大きな課題を抱えていた。
1つは人手不足だ。工場は24時間365日稼働しており、3交代のシフト勤務を行っているが、労働力人口の減少もあり、作業員の確保が難しかった。もう1つが、多品種少量生産、高品質な製品への要求が増加する一方、価格競争力のある製品を安定的に生産しなければならないというグローバル市場への対応である。
「当社の製品は、グローバルな競争にさらされている上に、季節変動や景気変動が激しいものも多い。特にパラダイムシフトの影響が大きい電子材料などは、市場が立ち上がったとき、すぐに安定供給できる体制をとらないとビジネスチャンスを失ってしまいます。しかしその一方で、多品種少量生産の機能性化学品の場合、どうしても熟練技術者の経験やノウハウに頼る属人的要素が多く、変動の激しい市場要求に合わせた高スキル人材の確保と育成が年々難しくなっていたのです」と住友ベークライトの稲垣 昌幸氏は打ち明ける。
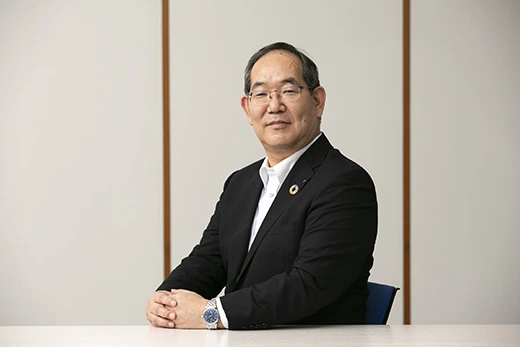
取締役 専務執行役員
稲垣 昌幸 氏
例えば、フェノール樹脂成形材料の生産工程では、フェノールレンジとガラス繊維、各種添加剤といった何十種類もの原料を混ぜ、熱を加えながら成分を均一に分散し反応することが品質を維持するための重要なポイントとなる。そのためにはスタート時の「温度」や「混合の回転数」、「圧力」などを、熟練技術者が原料の状態や経過時間を見極めながら、瞬時にコントロールする“匠の技”も必要であった。各ラインの生産設備の状態も均一ではなく、原料ロットの微妙な違いも含めると、暗黙知や経験による調整の選択肢は無限に近いものとなる。熟練技術者といえども現場で強いられるプレッシャーは非常に高いものがあったという。
「当社はSDGsの一環として、従業員がより快適に働ける環境整備やワークライフ・バランスの実現による持続可能なものづくりを志向しています。そのために作業員にかかる負担をいかに減らしていくかも重要なテーマでした」(稲垣氏)
そこで住友ベークライトは生産技術のデジタル化を推進することで、「人に頼らないライン(オートパイロット)」の確立を検討。そこには、属人的な業務を減らして生産効率を上げるとともに、多品種少量生産への要求が強まる中、安定した品質を担保しながら増産時の迅速なライン立ち上げを可能にする仕組みを確立したいという強い想いがあった。
DX化に向けたパートナーとしてNECを選択
同社でも「FA(ファクトリー・オートメーション)」「PA(プロセス・オートメーション)」「SIM(シミュレーション・インテグレーテッド・マニュファクチャリング/シミュレーション統合生産)」といったデジタル化は以前から行っていた。
だがそれは、ロット生産のように品種が固定化されたラインの生産効率は上げられても、多品種少量生産では、数百もある品番ごとにプログラムを入れ替えなければならず、変化への追従が難しい。
さらに、一定数量を品目ごとに連続して生産する「バッチ連続型生産」という特殊な生産ラインも、DX化に向けた大きなハードルとなっていた。
「生産ラインには以前からセンサーをつけていました。しかし機能性化学品では連続的な変化の中で機能や性能を出していくため、各センサーで採った瞬間値のデータと最終結果を相関させようとしても、その過程の、どの特性因子が関係したのかがはっきり解明できない部分もありました。属人性を廃した品質の安定化を実現するには、連続性のあるリアルタイムデータを収集できる仕組みをつくらなければなりませんでした」(稲垣氏)
この仕組みの実現に向け、同社はパートナーとしてNECを選択した。その理由を稲垣氏は「デジタル化に向けた構想企画のコンサルティングから、当社の課題に合わせたAIの実装、さらにはデータ分析までをワンストップで支援できる体制、何より、会社の垣根を越え一緒につくり上げていくという姿勢を評価しました」と語る。
リアルタイムなデータ収集とAI分析で自動制御を実現
2018年5月に立ち上がった共創プロジェクトは、3つのステップで進められた。
ステップ1は「全社共通の見える化(データ収集)」だ。
まずは生産設備の温度、速度、圧力といった稼働データや、製品となる樹脂材の厚みを測るセンサーを1ライン当たり既設を含め300~500個設置。工場の時系列データをリアルタイムに人手を介さず収集・見える化し、現場管理者や作業者が業務で活用できる仕組みを整備した。同時に、各拠点の稼働状況や生産実績を経営層がダッシュボードで把握できる環境も用意された。
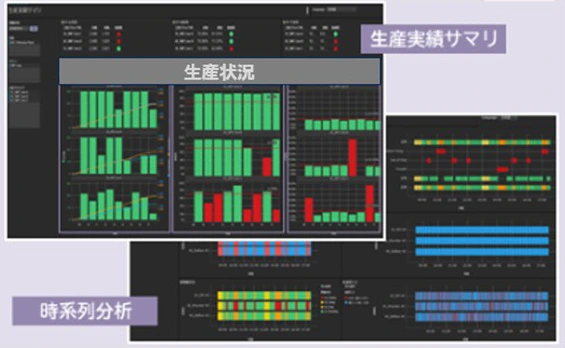
大量のセンサーから収集したリアルタイムなデータを一元的に集約・分析することで、生産状況や検査状況といった実績情報を時系列で表示できる仕組みを構築した
稼働データの収集プラットフォームに、「Edgecross(エッジクロス)」を活用。メーカーの異なる装置が混在していても通信規格の差異を吸収し、複数種類のデータを工場全体で分析できる環境を構築したのである。
ステップ2は「データ分析・トレーサビリティ強化」である。
ものづくりにかかわる各種実績情報(製番、原料、ロット№、プロセスデータなど)をひも付けた詳細なデータベースを構築し、統計分析やAI分析などで解析。さらなる品質改善に向けた施策の立案や現場改善、サプライヤーへの原料改善要求などに役立てることができる。また顧客から品質に関する問い合わせがあった場合も、スピーディな原因究明や対策検討につなげることが可能となる。
実績情報とNECの機械学習技術「インバリアント分析」を組み合わせて異常予兆検知も行っている。インバリアント分析とは、システムの特徴を表す普遍的な関係性を自動的かつ網羅的に抽出してモデル化し、そのモデルと一致しない“いつもと違う”挙動を監視・発見する技術である。この技術により、生産が安定した状態のデータと、リアルタイムな生産データを絶えず比較しながら、逸脱した異常予兆を検知することができる。異常があればアラームを発報し、生産ラインを自動停止するか、担当者を呼び出して対処にあたらせる仕組みだ。
ステップ3は、今回の目標の1つとなる「オートパイロット(自動監視/自律制御)」の実現である。
ここでは、あらかじめ各センサーから収集するデータに対して閾(しきい)値を設定しており、エッジPCに集まるセンサーデータと照らし合わせながら自動監視を実行する。また、運用上規定されている装置の制御ルールに加えて、AIの活用により熟練技術者の経験やノウハウに裏打ちされた装置制御に関する暗黙知を制御ルールとして登録する。この既存・新規の制御ルールに従って生産ラインは無人でも細かく自動制御できるようになり、生産性の向上と品質の安定化につなげていくという構想だ。
AIの分析により「これまでの常識」が覆されたルールも
機能性化学品の生産をIoTやAIでコントロールするという事例は、少なくとも日本ではほとんど例がない。それだけに両社はシステム開発でさまざまな苦労を重ねた。
「プロジェクトではNECのコンサルタントに企画・構想段階から入ってもらい、全体的なロードマップを策定した上で、現状把握から各ステップの進め方やルール、期限などを一緒に議論しながら進めていきました。同じ製造業といってもITと化学では使う言語や仕事の流れに大きな違いがあります。そのため最初はその壁を乗り越える相互理解からスタートし、しだいに共通言語でコミュニケーションしながら同じゴールを目指す良好な関係性をつくっていきました」と語るのは、オートパイロットの統括責任者を務めた住友ベークライトの野崎 隆二氏。
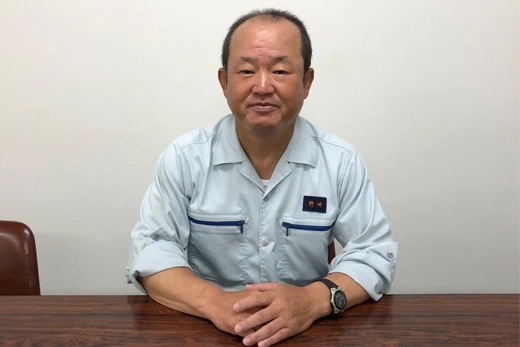
コーポレートエンジニアリングセンター センター長
野崎 隆二 氏
新システムではNECのさまざまなAI分析手法を組み合わせ、暗黙知となっていた未知のルールを既存の2倍以上、新たな制御ルールの仕組みに落とし込んでいった。その中ではこれまでの常識が必ずしも正しくないことがわかったという。
「熟練技術者の経験値では、ある工程で温度が上がり始めたらこのバルブを開く、といった独自のノウハウがあり、それが最適な手法だと信じられてきました。しかしNECのAIから導き出された新たな制御ルールでは、全く別なやり方で、より高品質な製品を安定的に生み出せるケースがあったのです。ファクトを裏付けるための数値化と、今までの思い込みを捨ててゼロからやることがいかに大事であるかを、改めて気付かされました」と、住友ベークライトでデジタル化を推進する櫻井 貴弘氏は語る。
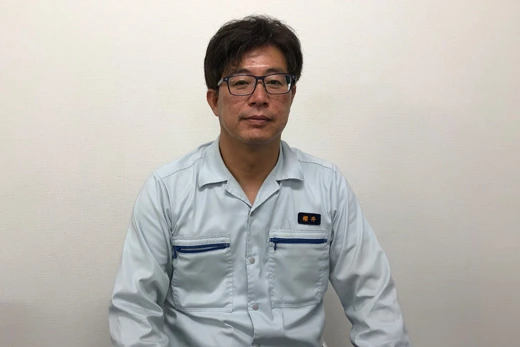
コーポレートエンジニアリングセンター
AI/IoT推進部 部長
櫻井 貴弘 氏
生産性が2割アップ。New Normalな生産体制にも有効なシステム
新システムは、2019年10月から九州住友ベークライトと静岡工場、2020年4月には尼崎工場、鹿沼工場でもそれぞれ稼働を開始した。
成果は既に表れている。各工場の生産ラインのメイン工程で、人的生産性が2割アップしたのがその一例だ。オートパイロットにより、熟練技術者の経験に頼らずとも安定した品質での連続生産が可能となり、これまで5人で行っていた作業が4人でカバーできるようになったのである。
「ムダな作業がなくなったため、ロスタイムも減りました。オートパイロットを適用したラインでは、稼働後一度も不合格品が出ておらず、大幅な歩留まり向上につながっています。今後さらにデータ蓄積が進めば、さらなる品質向上が望めます」と稲垣氏は満足感を示す。
貴重な熟練技術者を有効活用できるようになったことも大きい。今までは海外拠点での品質向上を図るため、定期的に熟練技術者を派遣していた。しかしオートパイロット体制がグローバルに確立すれば、国内からのリモート監視・制御が実現し、ベテランのスキルとノウハウを本来的なコア業務に振り向けることができる。
折しもシステムの稼働時期と新型コロナウイルスの感染拡大が重なったが、結果的にはラインの自動化・省人化による「3密回避策」として有効に機能した。同時に出勤する社員を従来の半分に抑えても、ラインを平常通りに稼働させることができたという。
「人をある程度減らした状況でも、生産を継続できることが確認できました。監視調整の業務なら、複数ラインや拠点を1人でカバーできるようになる可能性もあります。New Normalな生産体制にも有効なシステムだと思います」(稲垣氏)
今後、このシステムをほかの国内拠点やラインに展開する一方、2025年を目処に欧米・中国・東南アジアを中心とした海外工場でも稼働させる計画だ。
「既にデータ収集のためのセンサー設置は海外工場でも進めています。2025年には日本のマザー工場と同様の生産体制をつくり、各国から求められている住友ブランド製品の品質保証や納期保証を世界中で行えるようにしていきたいと思います」(稲垣氏)
さらにNECとの共創を通じて、DXに対応した人材育成も進めていく。材料系のシミュレーション技術に詳しい大学院生などを積極的に採用し、化学とITの両方の知見を持つ「ITケミスト」を養成。DXをさらに加速させる考えだ。
「最終的には、ロボティクスも含めて、さらなる省人化・効率化を進め、スマートファクトリーの実現とSDGsを両立させた次世代型のものづくりを推進していきたい」と語る稲垣氏。
これからもNECは、住友ベークライトをはじめとするさまざまな顧客との共創を通じて、New Normal時代における製造業のDXに取り組んでいく。
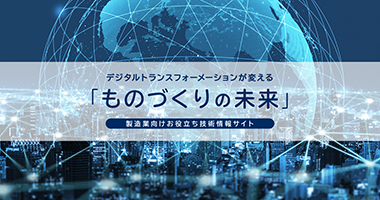