2016年01月29日
インダストリー4.0最新動向、日本・ドイツ・アメリカが目指す未来とは
インダストリー4.0の最新動向、日独米それぞれの取り組みを比較・考察する
インダストリー4.0で製造業、工場現場は何が変わるのか?
製造業(ものづくり)とICT技術が融合することで、インダストリー4.0(第四次産業革命)が起こると言われていますが、その意味と具体的な違いについて整理したいと思います。
これまでの製造業は、“製品”を開発設計して、予想した需要に基づいて生産計画を立て、工場で量産してきました。需要が変動すれば、これにあわせて生産ラインを増強し、人手を増やしてきたのです。
また、製品をリニューアルしたり、新製品を作ることで売上を拡大。保守やメンテナンスなどアフターサービスは、関連会社やパートナー会社が別途対応してきました。
しかし、最近では“製品”にセンサーを搭載してネットワークでつなげば、そのセンサーから得られるデータを使って稼働状況を監視したり、故障をあらかじめ察知(予知)したり、新しいソフトウェアを送ってアップデートすることで、これまでに無かった新しい機能を追加することなどが可能となりました。
スマートフォンやPC、自動車や建設機械、医療検査機器、工作機械など、既にいくつかの“IoT対応製品”が「モノ(製品)+コト(サービス)」を結びつけて提供しています。こうした“IoT対応製品”を製造している企業は、サービスを付加価値として提供することでサービス売上を上乗せして利益を増やし、稼働データを収集分析して新製品開発に活用することができます。
IoT技術は、「外向き(顧客向け)」に利用すれば顧客満足度(CS)を高めて売上高/収益に貢献する手段となり、「内向き(社内向け)」に利用すれば効率化や省人化などコスト削減を実現します。両方に取り組むことで、企業業績を飛躍的に高め、競争力を高めることができるのです。
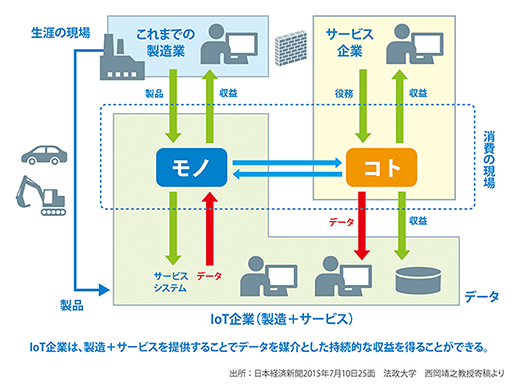
インダストリー4.0は、どちらかと言えば製造業における「内向き(社内向け)」の取り組みですが、その取り組みは製造現場に大きな変化をもたらすことになります。
従来型の工場では、“製品”を生産する工場や製造ラインは製品ごとに決まっていて、1つの製造ラインで複数の製品を作り分けることは困難でした。しかし、自動車や工作機械など、ユーザーのニーズにあわせて個別仕様の製品を作って欲しいという要望が増え、きめ細かな対応(マス・カスタマイゼーションと言います)が求められています。
これに対応した生産方式として、ドイツが提唱するインダストリー4.0では、「ダイナミックセル生産方式」という新しい生産方式を生み出しました。
これは、製品を生産する製造工程ごとに工場や製造ラインを切り替えることで、最終製品を作り分けるという考え方です。
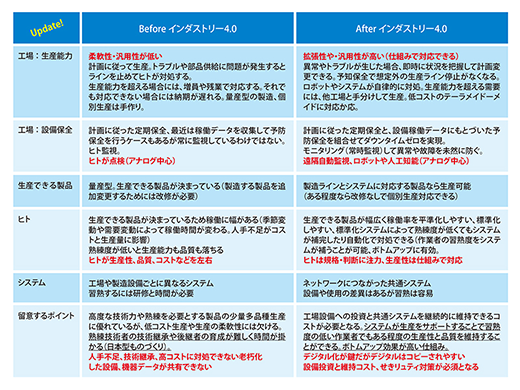
2015年にハノーバーで開催された産業見本市ハノーバー・メッセでは、シーメンス社が1つ1つ異なるオーダーを作り分けることができる香水の製造ラインを実演していました。ドイツのメルケル首相は、インドのモディー首相を招待してドイツの取り組みをアピールするとともに、製造分野における協力関係を進めています。
インダストリー4.0の同床異夢、戸惑う製造業と苛立つICT産業
世界に先駆けてドイツ政府は、中国やインドに対して積極的に製造分野における協力関係を推し進めています。また、米国は2014年にGE社など5社で創設したIICが2015年末には参加企業は200社超と急拡大しています。
日本企業ではトヨタ自動車、日立製作所、三菱電機、NEC、富士通などが、ドイツ企業もシーメンス、ボッシュ、SAPなどが参画して、世界の大手企業を巻き込んだ活動を展開しています。
IICは企業連合ですが、企業間の競争を是として、勝ち残った企業が総取りするデファクトスタンダードを掲げているため、市場をリードして主導権を握る競争が激しくなっています。
2016年1月に開催された世界最大の家電見本市CES2016(コンシューマ・エレクトロニクス・ショー2016、ラスベガスで開催)では、自動運転車やウェアラブル、ドローンなど、最新、最先端のIoT技術が組み込まれた商品やテクノロジーが大きな話題をよびました。米国企業の存在感と、圧倒的なパフォーマンスは新しい時代を予感するに足るものでした。
ドイツや米国の動きを見ると、インダストリー4.0の取り組みをはじめたばかりの日本からすると、羨ましくもあり焦燥感を抱くところですが、ドイツのインダストリー4.0に対する取り組みも予定通りに進んでいる訳ではないようです。
日本貿易振興機構(JETRO)の調査レポートによると、そのメリットである「生産工程の品質的改善」は想定通りですが、デメリットとして「高い投資コスト」(主に設備投資やその維持コストなど)、「複雑なテーマ」、「専門人材不足」(主にIT技術者)などが挙げられ、こうした分野では不満が高まっています。特に大企業と中小企業では温度差もあり、具体的なメリットを感じられない中小企業もあるようです。
また、製造業とICT系企業の間でスピード感にズレを生じていて、製造業側の慎重で正確性、確実性にこだわる姿勢が進捗の遅れを招いているとして、ICT企業側がしびれを切らしているとのことです。
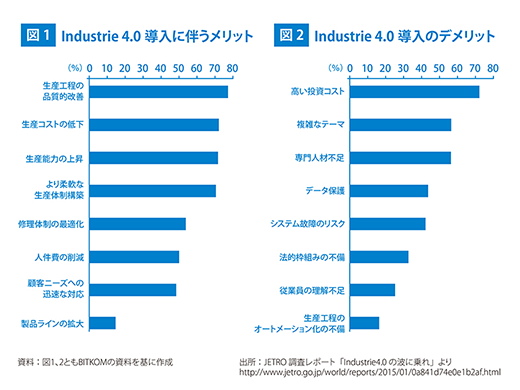
こうした悩みはいずれ日本においても、まったく同様の展開になることと予想されます。たとえば、製造現場では工作機械や治具など製造装置を最低10年以上使い続けることを前提として考えていますが、ICT側ではパソコンやコンピュータ類は2~3年程度で更新することが当たり前となっています。
5年以上前のコンピュータやソフトウェアでは、機能や性能がまったく違うことや古いシステムをサポートする技術者の確保や維持がコスト負担となり難しいのです。
実際にマイクロソフトなどいくつかの企業では、サポート期間を限定してこれを過ぎるとサポートを有償化したり、最新バージョン以外の製品はサポートしない、などとしています。
こうした業界慣習のギャップが顕在化して、先に紹介したような同床異夢の状況を招いているようです。お互いに歩み寄って、こうしたギャップを乗り越えるまでには、まだしばらく時間がかかるのかもしれません。
日本におけるインダストリー4.0への取り組みは、これから本格化しますが、一過性のブームのような状態を抜け出して、企業それぞれが中長期的な目標と戦略を策定して取り組むことになります。ここからは、何から取り組むのか、何を目指すのかを明確にして、腰を据えた取り組みが求められることとなります。先行するドイツや米国の動きを追いつつ、これに追従するだけでは勝ち残れない状況です。
日本の国内市場は成熟して、今後人口減少とともに衰退する可能性が高いと予測されていることからも、前に進む以外に選択の余地はありません。日本の製造業が置かれている状況は、この競争に勝ち抜かなければ生き残れない動乱の真っ只中に居るのかもしれません。